What is Magnetic Particle Testing (MT)?
Magnetic Particle Testing (MT) is a crucial Non-Destructive Testing (NDT) method. It helps detect surface and near-surface flaws in ferromagnetic materials. This technique plays a vital role in ensuring the integrity and reliability of components in various industries, including aerospace, automotive, and construction. In this article, we explore how MT works, its applications, and its benefits.
Magnetic Particle Testing is a non-destructive method that uses magnetic fields and small particles to find flaws on or near the surface of ferromagnetic materials. These materials include iron, nickel, cobalt, and some of their alloys. MT effectively identifies cracks, seams, inclusions, and other flaws that could compromise a component’s integrity.
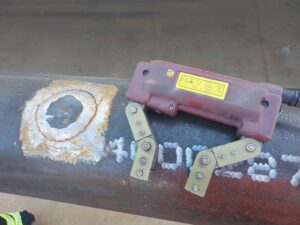
How Magnetic Particle Testing Works
Step 1: Surface Preparation First, clean the material’s surface to remove any dirt, grease, or other contaminants. This step ensures accurate detection.
Step 2: Magnetization Next, magnetize the material. Use either a direct method, where an electric current passes directly through the material, or an indirect method, where a current passes through a coil surrounding the material.
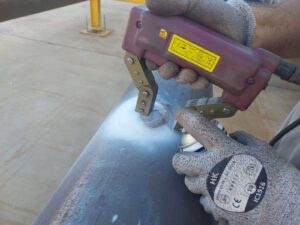
Step 3: Application of Magnetic Particles Then, apply small magnetic particles, either in dry powder form or suspended in a liquid, to the magnetized material’s surface. These particles gather at areas where magnetic flux leaks, indicating flaws.
Step 4: Inspection Finally, inspect the material under the right lighting conditions. Use regular lighting for visible particles and ultraviolet (UV) light for fluorescent particles. Flaws appear as clusters of magnetic particles.
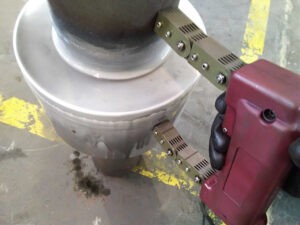
Applications of Magnetic Particle Testing
Magnetic Particle Testing is used in many industries to ensure the safety and reliability of critical components. Common applications include:
- Aerospace: Inspecting aircraft parts such as landing gear, engine components, and structural elements.
- Automotive: Testing critical parts like axles, crankshafts, and gears.
- Construction: Examining structural steel components, welds, and fasteners.
- Manufacturing: Quality control of castings, forgings, and finished products.
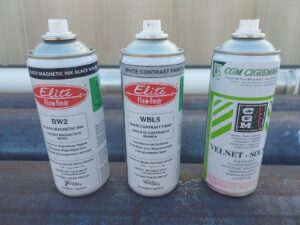
White Contrast Paint and
Solvant
Benefits of Magnetic Particle Testing
- High Sensitivity: MT can detect small surface and near-surface flaws.
- Quick and Efficient: The testing process is fast, allowing for the inspection of large areas quickly.
- Cost-Effective: MT requires minimal equipment and is less expensive compared to other NDT methods.
- Real-Time Results: Inspectors can see indications immediately, allowing for quick decision-making.
Limitations of Magnetic Particle Testing
- Material Limitation: MT is only suitable for ferromagnetic materials.
- Surface Preparation: Proper cleaning of the surface is essential for accurate results.
- Depth Limitation: MT is effective for detecting surface and near-surface flaws but not deep subsurface defects.
Conclusion
In conclusion, Magnetic Particle Testing is an invaluable NDT method for ensuring the integrity of ferromagnetic materials. By understanding how MT works and its applications, industries can enhance their quality control processes and maintain high safety standards. At SMART Consulting & Inspection, we offer expert MT services to help you detect flaws and ensure the reliability of your components.
Contact Us
For professional Magnetic Particle Testing services and other NDT solutions, contact SMART Consulting & Inspection today. Our experienced team is ready to assist you with your inspection needs.
Pingback: Essential Guide to NDT Techniques & ISO 9712 Standards -