Imagine observing Leonardo da Vinci’s Mona Lisa. Everyone knows the painting, but only a trained eye notices the subtle details — a faint veil, a hidden brushstroke, a shadow behind the smile. This idea, where small elements carry great significance, is exactly what we call the Detail Effect. In quality control, the smallest overlooked detail can impact product performance, reliability, and cost. Recognizing and sharing these details can transform routine work into measurable excellence.
How to Apply the Detail Effect in Your Quality Control Process
Ensure Proper Calibration
New tools, such as a digital thickness gauge, might arrive without a calibration certificate — unless you specifically request one. Without that document, even a 0.1% error could lead to major consequences: production stops, expensive rework, or unhappy customers.
That’s why calibration should never be assumed. Always check the documentation and confirm that your tool meets the required standards before use.
Proper calibration ensures measurement reliability and prevents costly errors.2. Minimize Human Error
Even the most precise tool is only as good as the hands that use it. For instance, applying too much pressure with a durometer can distort the reading by 2 to 3 HRC points. This doesn’t just alter the data — it could affect an entire production batch.
Therefore, it’s essential to train staff on consistent measuring techniques. In addition, peer reviews and occasional re-validation help keep human error in check.
3. Master Calibration Reports
A calibration certificate means nothing unless you know how to read it. For example, it may show that a measurement is “within range,” but fail to consider the uncertainty — the margin around the value.
Ignoring uncertainty can lead to poor decisions, especially when tolerances are tight. By understanding how to interpret calibration data, your team can avoid downstream issues.
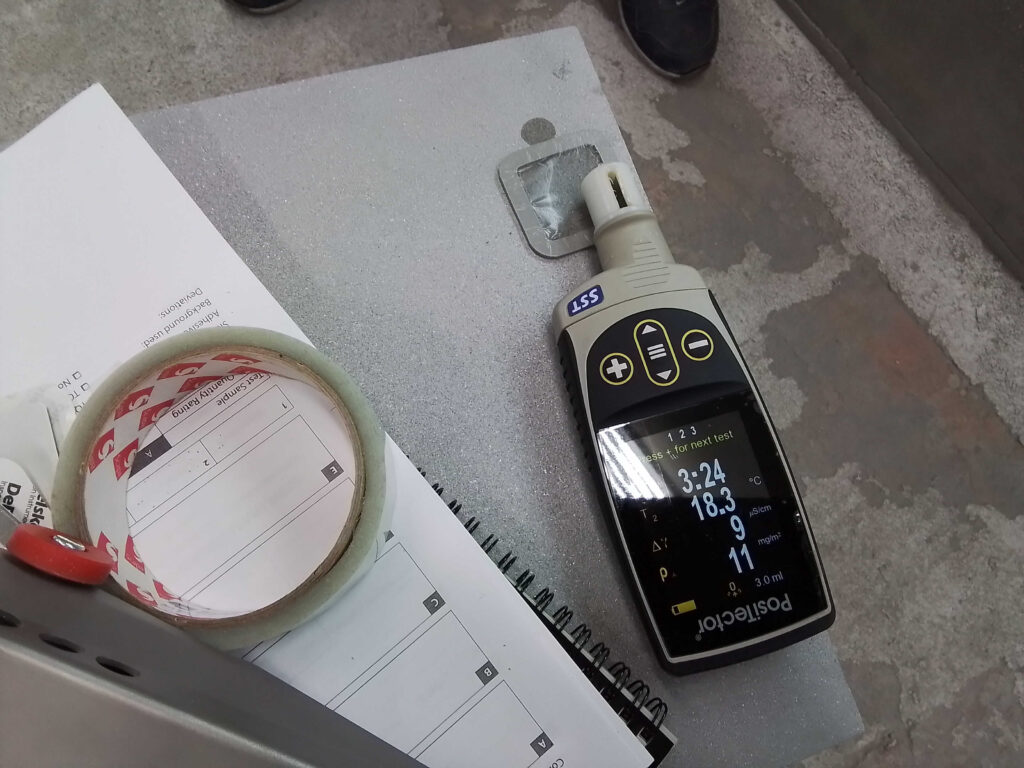
Why the Detail Effect Makes You Stand Out
This isn’t just about numbers. When you share overlooked insights, people start seeing you differently. You move from operator to expert — someone who drives change, not just executes it.
You earn respect. Showing how calibration affects costs or outcomes makes your perspective more valuable.
You simplify training. A concrete example — like “A miscalibration caused a 10,000-unit recall” — stays with your team longer than a rulebook.
You become the go-to expert. When someone says, “I hadn’t thought of that,” you’ve made an impact.
Moreover, these effects are contagious. Others start looking more carefully, and the team becomes sharper as a whole.
How Customers Benefit from the Detail Effect
Your clients may not know what a durometer is — but they will notice when products fail. That’s why quality isn’t just internal. It has visible, external consequences.
In short, attention to detail protects your brand. It builds trust. And it reduces complaints, delays, and frustration. Let your customers know:
“We check every detail to deliver products you can trust — every time.”
“Our process means fewer returns, fewer surprises, and better results.”
“Behind every product is a commitment to precision that lasts.”
Conclusion
In quality control, success doesn’t depend on luck — it depends on what you choose to notice. The Detail Effect is more than a mindset; it’s a tool for progress.
By sharing small but meaningful observations, you can strengthen your team, improve processes, and build customer confidence.
Ready to take your team’s quality mindset to the next level?
👉 Contact us today