Introduction
Pressure testing is a vital non-destructive testing method employed across industries to ensure that equipment operating under pressure maintains integrity and safety. This article will delve deeper into hydrostatic and pneumatic testing, including the use of helium for testing, explain how defects are detected, and outline compliance with the Pressure Equipment Directive (PED).
What is Pressure Testing?
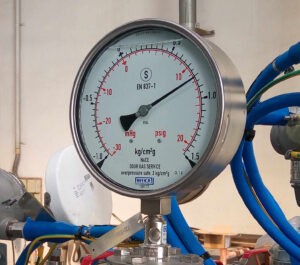
Pressure testing validates the structural integrity and pressure tightness of equipment like pipelines, boilers, and pressure vessels. It helps prevent potential operational failures by ensuring that these structures can withstand the operational pressures.
Hydrostatic Testing
Execution: In hydrostatic testing, the vessel or pipeline is filled with water, which is then pressurized to a specified test pressure—usually much higher than normal operating pressures—to ensure structural integrity.
Defect Detection: Defects during hydrostatic testing are typically spotted by observing a drop in pressure, visible leaks, or the use of dye penetrants that expose cracks and leaks.
Pneumatic Testing
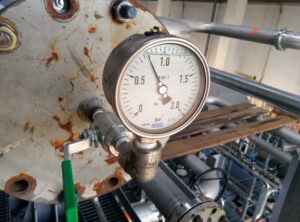
Execution: Pneumatic testing involves pressurizing a system with a gas, such as air, nitrogen, or helium. This method is chosen when the use of water could damage the system or when it is impractical.
Gases Used and Risks:
- Air: Commonly used due to availability and cost. The risk involves the potential for a violent release of energy if the system fails under pressure due to the compressibility of air.
- Nitrogen: Preferred in moisture-sensitive systems due to its inert nature, reducing the risk of corrosion and combustion. However, it poses an asphyxiation risk if leaked in a confined space.
- Helium: Used for its small molecular size, making it ideal for detecting very fine leaks. Helium is non-toxic, non-condensable, and non-corrosive, which minimizes the risk of damaging equipment or posing health hazards during tests.
Defect Detection:
- Air and Nitrogen: Typically detected through the formation of soap bubbles on applied surfaces or by listening for the sound of escaping gas.
- Helium: Detection involves using a mass spectrometer, which is highly sensitive to helium atoms. This method allows for the identification of even the smallest leaks due to helium’s ability to quickly escape through tiny openings.
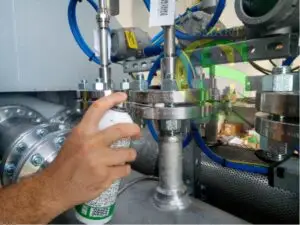
Comparing Hydrostatic and Pneumatic Testing
- Safety: Hydrostatic testing is generally safer due to the minimal energy involved with water.
- Application: Pneumatic testing is suitable when hydrostatic tests are unsuitable for the system materials or design.
- Detection Capability: Hydrostatic testing effectively identifies location and nature of leaks, whereas pneumatic testing with helium can detect even minuscule leaks.
PED Regulations
The Pressure Equipment Directive (PED) regulates the design and manufacture of pressure equipment in Europe to ensure safety.
Compliance Requirements:
- Adherence to strict design, manufacturing, and testing safety principles.
- Use of appropriate materials and verified construction techniques.
- Mandatory pressure testing before equipment is commissioned.
Practical Applications of Pressure Testing
- Quality Assurance: Ensures equipment is safe and ready for operation.
- Regulatory Compliance: Meets international safety standards, including the PED.
- Maintenance and Inspection: Helps in regular safety checks and preventive maintenance planning.
Conclusion
Choosing the right type of pressure testing—hydrostatic or pneumatic—depends on specific operational requirements and material sensitivities. With advancements in testing technologies, including the use of helium for fine leak detection, industries can enhance the safety and reliability of their pressure-operated equipment.
Contact Us
For comprehensive assistance in pressure testing and PED compliance, contact Smart Consulting & Inspection. Our experts are ready to support your needs with advanced testing solutions and expertise.